【導讀】激光切割加工具有切割精度高、切割速度快、熱效應低、無污染、無噪音等優(yōu)點,而激光切割加工質量與激光焦點與工件之間的相對位置有著密切的關系,保證激光焦點和切割對象之間的公道的相對位置是保證激光切割加工質量的關鍵之一。
激光聚焦的焦點位置無法直接丈量,但可以通過間接方法檢測。對于一個激光切割加工系統(tǒng),其焦點位置是由聚焦鏡的光學焦點 決定的,所以在聚焦鏡一定情況下其位置是不變的(不考慮聚焦鏡的熱效應),因此可以通過檢測聚焦鏡和被加工對象之間的相對位置來間接檢測焦點和被加工對象 之間的位置關系。
激光焦點和被加工對象之間的相對位置可以通過電感位移傳感器和電容傳感器來檢測,在使用中各有優(yōu)缺點。電感傳感器的響 應頻率較低,不太適用于高速加工和像!維加工這樣需要非接觸檢測的場合;電容傳感器,具有響應速度快,檢測精度高等優(yōu)點,但在使用過程中存在非線性和易受 激光切割加工過程中產生的等離子云和噴渣的干擾的影響。
本文將系統(tǒng)討論激光切割加工中激光焦點位置誤差的產生途徑和自動消除誤差的控制系統(tǒng)的組成。在此基礎上分別討論了兩種傳感器檢測系統(tǒng)組成以及實際使用中存在的不足和克服的方法。
1.激光切割過程中焦點位置誤差的產生
在激光切割過程中,產生焦點和被加工對象表面之間相對位置發(fā)生變化的因素很多,被加工工件表面凸凹不平、工件裝夾方式、機床的幾何誤差以及機床在負載力下的 變形、工件在加工過程中的熱變形等都會造成激光焦點位置和理想給定位置(編程位置)發(fā)生偏差。有些誤差(如機床的幾何誤差)具有規(guī)律性,可以通過定量補償 方法進行補償,但有些誤差為隨機誤差,只能通過在線檢測和控制來消除,這些誤差是:
1.1 工件幾何誤差激光切割的對象 為板材或覆蓋件型零件,由于各種原因的影響,加工對象表面具有起伏不平,且在切割過程中的熱效應的影響也會產生薄板零件的表面變形,對于1維激光加工,覆 蓋件在壓制成型過程中也會產生表面的不平,所有這些,都會產生激光焦點與被加工對象表面的位置與理想位置發(fā)生隨機變化。
1.2 工件裝夾裝置產生的誤差
激光切割加工的工件是放在針狀工作臺上,由于加工誤差、長時間與工件之間的磨損和激光的燒傷,針床會出現(xiàn)凸凹不平,這種不平也會產生薄鋼板和激光焦點之間的位置的隨機誤差。
1.3 編程產生的誤差在1維激光切割加工過程中,復雜曲面上的加工軌跡是通過直線、圓弧等擬合的,這些擬合曲線和實際曲線存在一定誤差,這些誤差使得實際焦點和加工對象表面的相對位置和理想編程位置產生一定誤差。而有些示教編程系統(tǒng)也會引進一些偏差。
2.激光切割過程中焦點位置在線檢測與控制系統(tǒng)的組成
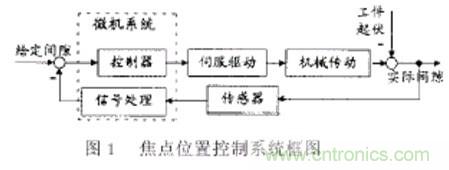
如圖1所示,激光切割焦點位置在線檢測與控制系統(tǒng)由控制器、檢測系統(tǒng)、執(zhí)行裝置等部分組成。
根據(jù)焦點位置檢測控制系統(tǒng)和系統(tǒng)的關系,焦點位置檢測控制系統(tǒng)分為獨立式和集成式兩種。獨立式焦點位置檢測與控制系統(tǒng)采用單獨的坐標軸進行焦點位置誤差的補償控制,機械結構復雜,本錢較高,但可與各種數(shù)控系統(tǒng)和激光切割機床配合使用。而集成式采用激光切割機床本身的一個進給軸(對平面加工)或多個進給軸的合成(對于1維切割加工)運動來進行焦點位置誤差的補償。這種方式具有結構簡單、本錢低,易于調整等優(yōu)點,但要求和數(shù)控系統(tǒng)同一設計,對數(shù)控系統(tǒng)的開放性要求較高。
2.1 電容傳感器檢測電路
如圖2所示,電容傳感器檢測電路由調諧振蕩器、信號放大器、晶體穩(wěn)頻振蕩器、同步電路、混頻電路、信號處理電路等將電容量信號變成對應頻率的脈沖信號,通過 對脈沖信號進行頻率采樣和處理,得到相應的電容量。這里的電容為切割噴嘴和切割對象之間兩個極板形成的電容。顯然其電容量除了與兩個極板的面積有關外,還 與極板之間的介質、極板之間的間隔有關。而這個間隔就與激光聚焦鏡和工件之間的間隔有關,也就是與激光焦點與工件之間的間隔有關,所以電容量近似和焦點位 置與切割對象之間的間隔有關。這就是電容傳感器檢測焦點位置的原理。
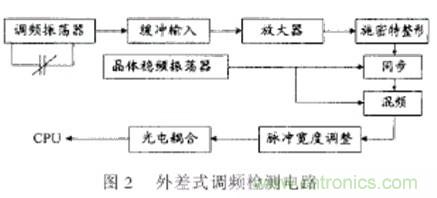
從圖中可以看出,頻率和焦點位置誤差之間的關系為非線性關系,必須通過計算機進行線性化處理。同時,由于電容量還和極板之間的介質有關,所以檢測結果輕易受加工過程中產生的等離子云和噴渣影響,必須加以克服。
2.2 電感傳感器檢測電路
如圖3所示,由于采用了最新的大規(guī)模集成電路,電感傳感器的檢測電路比較簡單,且集成電路采用了新的調制解調方法和算法,減少了以前的檢測外差式調頻檢測電路方法由于傳感器的激勵信號的相角、頻率以及幅值漂移對檢測結果的影響,大大進步了檢測精度和穩(wěn)定性。
傳感器信號通過處理后得到與傳感器測頭位移成正比的電壓信號,通過變換電路轉換成相應的頻率信號,通過計算機處理得到了焦點的位置誤差信號。
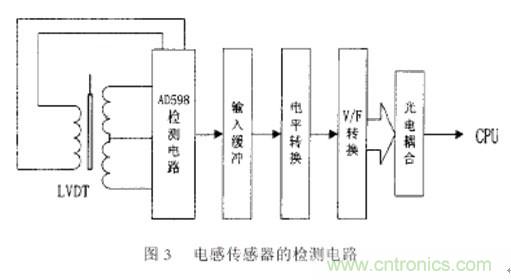
由于電感傳感器的固有特性,對被測信號的頻率有一定的限制(幾百),不太適用于高速加工場合,同時,由于其為接觸式檢測方式,只能用于平面加工場合。
3.切割過程中等離子云對焦點位置檢測系統(tǒng)的影響
在工件尚未被切穿的瞬間,激光和金屬相互作用,在噴嘴和加工對象之間產生云霧狀等離子體,改變電容極板之間的介質,從而對電容傳感器產生干擾。在正常切割過 程中,輔助氣體將等離子體從切縫中吹散,對電容傳感器產生影響較小。但假如加工速度太快和剛開始切割時,由于工件未被完全切穿,激光照射點四周會產生等離 子體云,對電容傳感器產生干擾,嚴重時甚至使傳感器無法正常工作,嚴重影響加工質量。圖4為等離子體干擾示意圖。
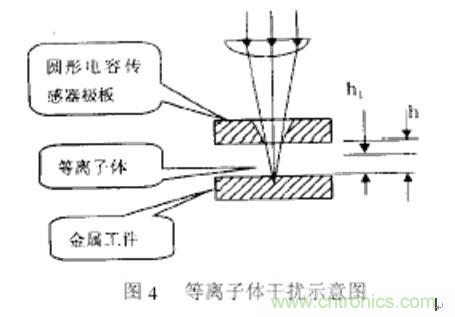
由電磁學原理可知,相鄰的兩個極板間電容量為C=εS/h, 式中ε---極板之間介電常數(shù))一般為(1), S---極板相對有效面積, h---兩極板間間隔, 假如沒有等離子體的干擾,那么,根據(jù)式(1)所測到的電容就和極板(噴嘴和加工對象)之間間隔成反比,由電容量可以方便求出兩極板間間隔,進而求出焦點和被加工對象之間的相對位置。但是,當噴嘴和被加工對象之間存在等離子體或噴渣時,電容極板之間的電介質就不是空氣了,其介電常數(shù)就發(fā)生變化。由電容原理公式,此時兩個極板間電容量為:
C''''=ε S1 /[(h-h1)+h1ε/ε1 ]+εS2/h (2), 式中ε1---等離子體的介電常數(shù), h1---等離子體云的厚度, S1 + S2 =S分別為有等離子云或噴渣的區(qū)域和無等離子云或噴渣的區(qū)域的面積, 假如等離子云均勻分布于噴嘴和被加工對象之間的一定高度范圍之內,則電容傳感器所測得的兩極板間間隔為:
h''''=(h-h1)+ h1ε/ε1 (3)
檢測的誤差理論值:
Δh = h''''-h
= h1 (ε/ε1 -1) (4)
從 式(4)可知,誤差的大小由極板間等離子體云的厚度及等離子體的介電常數(shù)決定。而等離子體介電常數(shù)具有非常大的值,可以達到105的數(shù)目級。所以由式 (4)可以看出等離子云或噴渣對檢測結果的影響是非常大的,文獻[2~4]得出,假如等離子體云的厚度為1~2mm,則由電容傳感器檢測的兩極板間間隔的 理論誤差也達到1~2mm,顯然達不到激光焦點位置檢測的精度指標(為±0.2mm)。
4.傳感器優(yōu)化設計技術減少等離子云對檢測結果的影響
等離子體對電容傳感器的干擾是由于等離子體改變了電容兩極板之間的介質。因此,為了消除等離子體對電容傳感器的干擾,就要使電容兩極板之間的介質不受等離子體的影響,可以加大圓環(huán)形極板的中心小孔和將電容傳感器移至等離子云以外兩種方法來實現(xiàn)。
(1) 要消除等離子體對電容量的影響,就要將等離子體置于電容傳感器的極板之外??紤]到等離子云是沿切割點四周分布的,因此可以如圖5所示:將圓環(huán)形極板的中心 小孔直徑擴大至2~3mm并嵌進盡緣的耐高溫陶瓷材料,由于電容傳感器極板是空心的,在不考慮邊沿效應的情況下,照射點四周的等離子體云對傳感器電容量和 檢測值不產生影響,所以采用這種辦法能有效地減小等離子云的干擾影響。
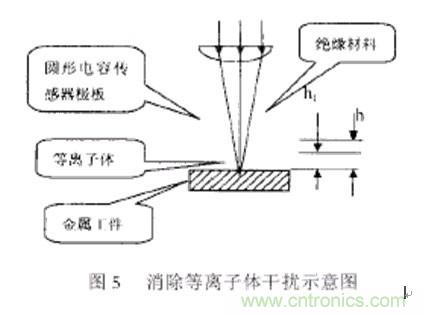
(2) 對于平面激光切割加工,還可以通過機械傳動方法進行間接丈量。即通過一機械裝置跟隨被加工對象運動,將機械裝置的上端和檢測傳感器形成極板,通過檢測傳感 器和這個機械裝置之間的間隔來間接檢測激光焦點和被加工對象之間的位置。這種方法可以最大限度避免了離子云和噴渣對檢測精度的影響,也發(fā)揮了電容傳感器響 應迅速的優(yōu)點。
5.結論
激光焦點位置檢測與控制是激光切割加工的關鍵技術之一,對于快速切割加工,焦點位置檢測精度和快速性將直接影響到焦點位置的控制精度和加工質量,電容傳感用具有檢測靈敏度高、響應快速的優(yōu)點,可以通過計算機系統(tǒng)的線性化來克服其非線性;通過特殊的傳感器結構來消除加工過程中產生的等離子云和噴渣對檢測結果的影響,進步其在激光切割加工系統(tǒng)中的使用效果。