【導(dǎo)讀】油電混合動力汽車和電動汽車逐漸獲得大家的認(rèn)可,這為電子行業(yè)創(chuàng)造了大量機(jī)遇。雖然近年來電子元件在典型汽車物料單中所占的比例逐漸提高,但是采用電力牽引可能是將現(xiàn)代汽車塑造成一種電氣裝置的顯著進(jìn)步。
作為油電混合動力或純電動汽車高壓基礎(chǔ)設(shè)施的一部分,IGBT逆變器功率模塊是用于控制牽引電機(jī)的電傳系統(tǒng)的關(guān)鍵元件。典型模塊包含1個三相全橋逆變器,其由6個IGBT開關(guān)和若干續(xù)流二極管組成,如圖1所示。幾個IGBT器件可以用在各個開關(guān)位置,以便實現(xiàn)所需的額定電流和通態(tài)電阻。
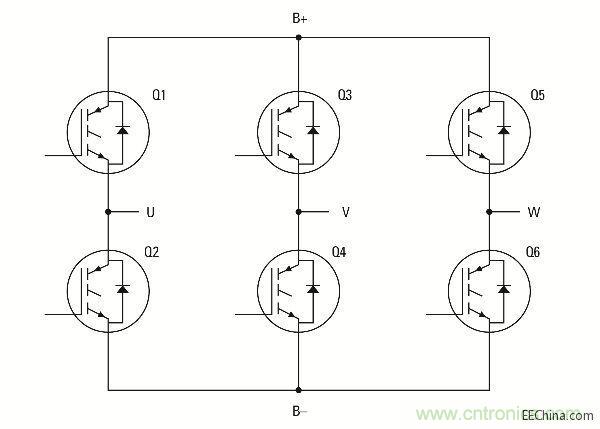
圖1:典型HEV/EV功率模塊的三相逆變器。
如果電機(jī)的額定功率為100Kw(相當(dāng)于134馬力),那么效率高達(dá)97%的模塊會主要以熱的形式耗散掉3kW左右的能量。如果模塊要提供令人滿意的可靠 性,那么有效去除該熱量是關(guān)鍵?,F(xiàn)代內(nèi)燃機(jī)汽車已經(jīng)設(shè)立了很高的可靠性標(biāo)準(zhǔn),而電動汽車必須達(dá)到這些標(biāo)準(zhǔn)方可獲得廣大消費(fèi)者的認(rèn)可。
提高模塊可靠性
提高模塊可靠性和額定功率的措施包括采用裸片IGBT和優(yōu)化模塊結(jié)構(gòu),進(jìn)而將導(dǎo)致焦耳加熱的寄生電損耗降至最低水平,在IGBT晶圓和模塊基板之間實現(xiàn)最低的熱阻。
與第一代油電混合動力汽車采用的功率模塊相比,如今模塊的典型熱疊加被大大簡化,從而將晶圓和模塊基板之間的熱阻降至了最低水平?;蹇赡軒в写罅可崞?以實現(xiàn)空氣冷卻,或者更常見的則是利用水/乙二醇混合物進(jìn)行液體冷卻。典型現(xiàn)代IGBT功率模塊的熱疊加和電觸頭如圖2所示。
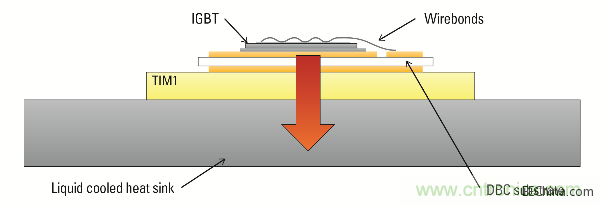
圖2:典型IGBT功率模塊的構(gòu)造。
至于IGBT,適用于現(xiàn)代大功率應(yīng)用的器件需要高達(dá)300A(或更高)的電流處理能力。這導(dǎo)致晶圓尺寸大至100mm2(或更高)。此外,最新一代器件采用超薄晶圓技術(shù)制造而成,晶圓厚度為100?m(或更低)。這樣就將電路徑長度降至了最低水平,從而進(jìn)一步提升了通態(tài)性能,還降低了載流電荷,有助于提高開關(guān)效率。超薄晶圓技術(shù)還增強(qiáng)了散熱。
然而,超薄晶圓為模塊制造商提出了艱巨的生產(chǎn)挑戰(zhàn),最終會導(dǎo)致產(chǎn)線良率降低。模塊通常采用裸IGBT晶圓裝配,從而抵消了任何二次封裝相關(guān)的無晶圓封裝電 阻(DFPR)和封裝熱阻(RTHj-c),進(jìn)而提高了能源效率和熱性能。在被從載流中彈射出來時或者在后續(xù)處理過程中,大型超薄芯圓可能會折斷。[page]
可能要使用特殊處理設(shè)備,但是當(dāng)模塊暴露在熱循環(huán)中時,晶圓尺寸大可能會直接影響可靠性。晶圓尺寸大會導(dǎo)致晶圓與模塊基底之間CTE嚴(yán)重失配,從而在焊接 的管芯連接接頭或晶圓上產(chǎn)生較大的應(yīng)力。多次熱循環(huán)之后,管芯連接接頭會退化,從而導(dǎo)致IGBT晶圓和基底之間的熱阻增加。這會造成過熱,進(jìn)而降低性能, 最終導(dǎo)致模塊過早損壞。
制造商可以通過將晶圓焊接到直接鍵合銅(DBC)基底上來降低材料之間CTE失配對結(jié)構(gòu)的影響。這類裝配用鋁焊線(見圖2)將IGBT發(fā)射極連接到模塊終 端上,通常會使用幾根直徑介于0.25mm(0.01英寸)和0.5mm(0.02英寸)之間的粗導(dǎo)線??煽啃詼y試表明,焊線和前敷金屬之間的接口很容易 疲勞,因此限制了模塊的使用壽命。
在最終測試時,模塊制造商遇到了另一個挑戰(zhàn)------生產(chǎn)率。他們在封裝前通常無法在全工作電流下測試功率半導(dǎo)體芯片。因此,某些與裸片有關(guān)的故障可能只有在已裝配模塊的最終測試期間才能發(fā)現(xiàn),這就降低了良率。
同一封裝內(nèi)的裸片性能
國際整流器公司(以下簡稱“IR”)的COOLiR2Die是一項新型封裝技術(shù),旨在彌補(bǔ)傳統(tǒng)裸片裝配的不足。這種封裝技術(shù)中的晶圓直接附于CTE與硅類 似的DBC基底之上。該基底為晶圓提供機(jī)械支持,消除了對焊線的需求,還實現(xiàn)了雙面冷卻,進(jìn)而提升了熱性能。器件采用卷帶封裝,可利用傳統(tǒng)SMT設(shè)備進(jìn)行 放置。
晶圓電極鍍有銀,使其易于焊接。這就是它與鍍鋁或鋁合金的傳統(tǒng)絲焊模塊使用的芯片之間的關(guān)鍵區(qū)別。消除焊線除提高了可靠性,還提升了電性能。周邊集電極凸點(diǎn)和晶圓背面的電極之間的電阻約為48??。利用6根直徑為0.5mm的鋁焊線實現(xiàn)的典型連接的總電阻超過140??。
利用這種封裝技術(shù),IGBT可實現(xiàn)倒裝晶圓或晶圓朝上配置。倒裝晶圓配置如圖3所示,由IGBT和二極管構(gòu)成,二者均翻轉(zhuǎn)過來,所以IGBT的柵極和發(fā)射 極以及二極管的陽極都附在DBC基底上。管芯連接材料可以是高鉛焊料,也可以是面向無鉛應(yīng)用的燒結(jié)銀材料。IGBT的發(fā)射極和柵極以及二極管的陽極通過 DBC基底的導(dǎo)電線與周邊觸點(diǎn)相連。
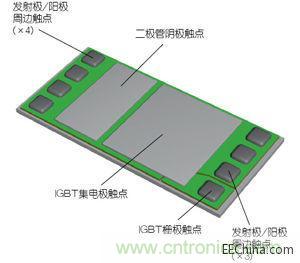
圖3:倒裝晶圓裝配
在晶圓朝上配置(如圖4所示)中,發(fā)射極和柵極都正面朝上(因此稱為“晶圓朝上”),而IGBT集電極和二極管的陰極則與周邊觸點(diǎn)相連。
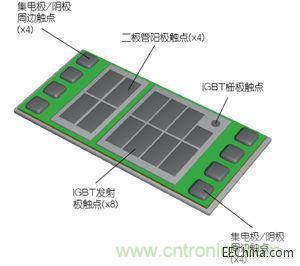
圖4:晶圓朝上裝配
借助于倒裝晶圓和晶圓朝上配置,模塊制造商可以利用模塊DBC基底的銅絲(見圖5)來連接倒裝晶圓IGBT的發(fā)射極和晶圓朝上器件的集電極,進(jìn)而有效地構(gòu)建半橋或全橋電路。
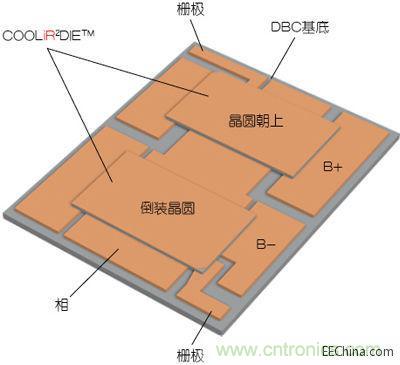
圖5:半橋模塊內(nèi)的倒裝晶圓和晶圓朝上IGBT
COOLiR2Die DBC基底有幾種功能。除了為超薄晶圓提供機(jī)械支持,它還在晶圓表面的電極和封裝的周邊終端之間實現(xiàn)了低電阻/低電感互 連,保證晶圓與封裝背面之間電絕緣。DBC的電介質(zhì)芯可以是氧化鋁(Al2O3)、氮化鋁(AlN)或氮化硅(Si3N4)。材料的選擇及厚度取決于成本 以及熱和可靠性要求。Al2O3是一種成本較低的電介質(zhì),CTE低且接近于硅,而AlN和Si3N4的CTE與硅更接近,但成本較高。[page]
在晶圓附于DBC基底上時,IGBT和二極管電機(jī)之間的大接觸面積以及DBC上的導(dǎo)電線有助于在晶圓和封裝正面之間提供低熱阻通道。由于封裝的頂部是電絕 緣的,所以模塊制造商可以借此機(jī)會利用如圖6所示之布局進(jìn)一步提升熱性能。在該圖中,模塊蓋用作散熱器,其通過熱界面材料(TIM)與封裝正面實現(xiàn)熱耦合。
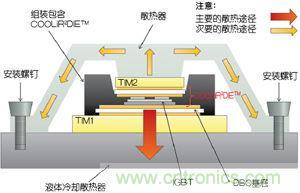
圖6:利用絕緣封裝正面增強(qiáng)了冷卻效果
根據(jù)晶圓尺寸,COOLiR2Die器件的生產(chǎn)工藝包括高達(dá)500A(或更高,如果需要的話)的大電流測試。這能夠幫助那些需要將多個晶片裝配到逆變器基圓上的用戶提高模塊產(chǎn)量。
為了構(gòu)建模塊,傳統(tǒng)SMT置放機(jī)可以用來放置元件,周邊終端和IGBT與二極管電極朝下,這樣就能夠?qū)⑵浜附拥侥KDBC基底上去。然后進(jìn)行回流焊。對于那些需要3-5%或更低的焊接空洞的大功率應(yīng)用而言,建議采用真空回流焊。
結(jié)論
油電混合動力和電動汽車技術(shù)不斷發(fā)展,旨在提高效率、功率和可靠性,而這項新技術(shù)有助于消除焊線,提高裝配率,簡化生產(chǎn)逆變器功率模塊所需的工藝和設(shè)備。